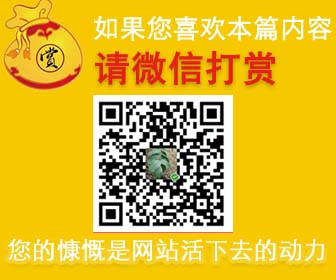
拔长、倒棱、滚圆等作为大型轴类锻件最基本的锻造工艺是决定锻件质量的关键,而国内外有许多学者在工艺优化方面做出了重要的研究成果。现在大多数的研究都是对锻造工艺中不同的工艺参数对锻件的质量影响,比较经典的是上海交通大学的付强等人对300MW 汽轮机低压转子典型的锻造过程进行了数值模拟,选用平砧拔长的方法对圆截面坯料进行锻造,研究了压下量与表面成形质量,以及不同的上下砧圆角及锻造过程中的接砧量对锻件性能质量的影响[1]。山东大学的李锦等人用 DEFORM软件 对不同镦粗工艺模拟发现凹形坯料镦粗或先端面压凹再平板镦粗均在不同程度上提高了变形均匀性 ,解决了自由镦粗易鼓形的问题[30]。为了改善锻件拔长出现的变形不均匀性,减少压机工作载荷,太原科技大学的栗玉杰等人针对其锻造中拔长过程,研制开发了一种新的砧型新型凸面砧[6]。孔洞型损伤是大型锻件缺陷的主要形式,华南理工大学型程秀全,霍育林等人,采用有限元数值模拟的手段得出了电液锤的打击能量对孔穴锻合的影响很小;而压下量的大小直接决定孔穴的闭合程度[35]。在倒棱滚圆方面的研究成果并不多,其中比较突出的是来自上海交通大学的付强等人以不同型砧设置了参数,对大型锻件的锻造过程进行数值模拟研究了最后在平砧,90V砧和120V砧不同情况下锻件的成形尺寸,以及重点关注了其应变场的分布状态,得出倒棱滚圆方面的成形质量最好的是120V砧的情况[8]。25895
上面主要表明当下大多数学者对于锻造的研究多集中在锻造工艺上不同的参数对锻件质量上的影响,模锻的成形方法简单又容易操作,而且效率非常高,且由于其独特的加工过程,主要是将金属胚料在锻压作用下压成模具的形状,所以这也决定了模锻独有的加工余量小,尺寸精确,又不会造成材料的浪费,最后也是很重要的一点就是,由于锻件是按模具内轮廓流动分布,所以最后生产出来的产品也会使用寿命长,且表面成形好,力学性能优良,但是相比自由锻,模锻所用到的模具花费大,投资巨大的特点,所以研究模锻成型过程,优化工艺,减少前期投资以及模具损伤成本,提高锻件质量已经成为一个重要的课题。论文网
南华大学李晔在他的论文里详细的介绍了传统的开式模锻与闭式模锻,针对两种工艺的有点和不足,取长补短,提出了先闭后开式以及半闭式模锻两种优化工艺设计,促进了模锻行业的质量水平的飞速提高[41]。在斗齿闭式模锻工艺研究方面,比较有代表意义的是福州大学的顾勇,在数值模拟的基础上,提出了可行性的优化工艺方案[42]。叶焕君提出了热模锻模具飞边槽深与桥部宽之比为1:3.2的优化设计方案[43]。陈瑞钢,崔慧然通过对典型壳体件模锻工艺的特点,取消了制坯工步,模具优化设计,从而改进了此类工艺上的缺点,降低了生产成本[45]。缸头是一种结构很复杂的零件,应用模锻加工时,成形过程出现充不满、折叠等缺陷的几率很大,这个对实际生产影响很大,此问题一直亟待解决,对此来自福州大学的江星莹等人对其成型过程建模,并且对其最终成形尺寸,形状,和内部金属的流动做了数值分析,最后改进了预制坯形状尺寸[46]。胡杰和刘凯泉以锻钢曲拐为研究的对象并且三文建模且对其模锻成型中的应力场进行了研究,以后再研究曲拐模锻就会有更详细的资料[ 锻件锻造工艺研究现状:http://www.youerw.com/yanjiu/lunwen_19883.html