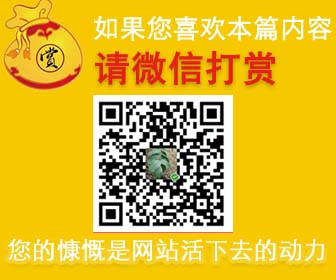
断续切削国内外实验研究现状断续切削技术是一项先进制造技术,其研究可追溯到20实际40年代末。对于断续切削研究,国内外专家主要是从断续切削过程中切入和切出破损方面研究,包含切出过程中负剪切现象的动态切削力的研究,切削力、热应力和热裂纹的研究、以及刀具的几何参数等等。1946年德国学者M.Kronenberg率先提出了通过端洗加工,研究切入类型与刀具磨损之间的关系,在进行了大量的实验切削实验和进行过程模拟,解决了切入类型的计算问题,并提出了九种切入类型的判别公式和定义了切入角。49499
到了1999年,我国学者董丽华、李振加等通过不同角度的铣刀片进行有限元应力场分析,证明了合理的刀具几何角度可以改变切入冲击力的方向,减少刀片内部应力;2005年李振加等人依据金属切削加工理论,在M.Kronenberg接触法和林树兴几何解析法的基础上,研究了端面铣削过程中刀齿的接触情况,推倒了九种判别式,用于计算铣刀的切入类型;同年,胡映宁、王成勇等人采用动力学仿真软件对小直径铣刀在不同切削参数条件下切入过程进行了仿真分析,确定了小直径铣刀切入过程的载荷、运动形式,根据仿真的载荷结果,勇有限元分析确定不同切削参数下,铣刀的切入过程对刀刃的应力、变形的影响,为寻求合理的切入条件,减少刀具破损提供了参考。
在研究刀具破损寿命时, 研究人员长期以来沿用静态切削力代替动态切削力的传统方法不可避免地导致理论预测与实验数据的偏差。为了准确地预测刀具破损寿命, 迫切需要对切削力的动态变化规律进行研究。对于切削力的研究, 许多学者做过不少工作。Das and Tobias建立了一个模型论文网, 他们假设切削力和剪切力是剪切面积的线性函数及出现迅速振动时, 剪切面不随工件的移动而变化。后来, 通过高速摄影证实在动态切削中剪切面也在不断变化.Nim等建立的模型考察了切削参数的动态变化对剪切面振动的影响。近来,Wu和Liu进一步基于加工硬化和滑移线场理论并考虑剪切面和刀屑接触面的应力状况推导出一系列公式[1]。
断续切削中, 脆性刀具材料产生的热破损和机械破损都是难以避免的问题。Mc.Shaw,Loladze和Pakelhuring等学者对刀具破损从机械方面原因进行了研究。KunioUoharo,H.Chandrasekaran,C.W.Merten和B.F.Vonturkovich等学者研究了切削刀具的温度梯度和相应的应力场[2]。认为断续切削中, 由热应力所引起的梳状裂纹导致刀具破损, 这一观点已得到验证。此外,许多学者认为, 热裂纹形成于切出阶段,认为刀具在工件上切削时,在刀具表面与其内部之间产生很陡的温度梯度, 形成压缩热应力,由此导致裂纹产生,当刀具切出时,其表而突然冷却, 刀具表面温度比内部温度低,产生拉应力,并引起裂纹扩展,这一论点已被许多学者所接受。
断续切削国内外实验研究现状:http://www.youerw.com/yanjiu/lunwen_52488.html