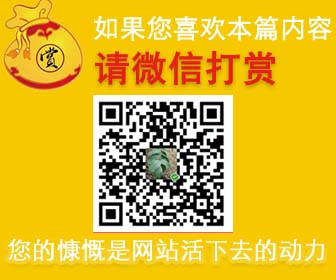
图1-1 单摆法测量熔融物反冲压力
然而,随着孔深度的增加,反冲压力逐渐减小,熔融物没有足够动力离开小孔,在沿壁面的流动中逐渐冷却。打孔结束后,孔内有重铸层[14],导致了小孔形状不规则,甚至有时孔口被堵塞[15],因此,如何将毫秒激光应用于精密加工,并且提高加工工艺及效率,是迫切需要解决的问题。
若要提高小孔质量和打孔效率,关键在于提高质量迁移率,也就是进一步促进熔融物离开小孔。目前,主要的解决方法有两种,一种是借助外部力量,即向孔内喷入高压辅助气体[16];另一个是改变作用激光参数,包括对激光脉冲整形,采用双脉冲或多脉冲联合打孔的方法[17]。不过,在一些特定情况下,例如作用远距离目标时,或者加工需要真空环境时,只能采用后一类方法。
双脉冲联合打孔的思路在于,第二个激光脉冲可以起到增加反冲压力作用,从而提高物质迁移的质量,这一般表现于材料更易被打穿。不过这里双脉冲并没有确切的脉宽组合形式,而是根据不同需求存在多种组合。Fox[18]首先提出了利用连续激光和纳秒激光联合打孔。但Lehane和Kwok[19]认为纳秒激光将产生等离子体屏蔽效应,影响激光与材料的相互作用,因此提出毫秒激光与百微秒激光的组合。后来又陆续出现双纳秒脉冲组合以及百微秒激光与纳秒激光组合[20]。因为毫秒激光作用下质量迁移率较高,所以取第一个脉冲的脉宽为毫秒,下面将讨论第二个脉宽的选择。
首先,可以从上述脉冲组合中发现,第二个脉冲的宽度总小于或等于第一个脉冲宽度,所以将候选脉宽限定在纳秒到毫秒脉宽之间。进一步的,在这个范围内,选择合适的脉宽。也就是说,在这个脉宽激光作用下,质量迁移可以得到最大的提升。Allmen [21]的研究指出,反冲压力值略大于饱和蒸气压的一半,而后者则与蒸汽温度有关;当激光功率密度达到108W/cm2时,反冲压力约为480atm。实际上,继续提高激光功率密度,蒸气将发生电离从而产生等离子体。相关研究表明,等离子体爆轰波(Laser-Supported Detonation Wave)作用在材料表面的压力可以达到约1500atm[22]。可见,在等离子冲击波作用下,熔融物应当能够被迅速挤压出小孔。与毫秒及百微秒激光相比,纳秒激光功率密度相对较高,容易产生等离子体。同时,纳秒激光与材料相互作用时间短,热影响范围小,不会进一步增加熔融物。结合这两个方面,可以确定选取纳秒为第二激光脉冲的脉宽,如图1-2所示。在等离子体爆轰波对材料表面的压力和反冲压力的联合作用下,熔融物将更容易被挤压出小孔,如图1-3所示。
图1-2 双脉冲联合打孔示意图。 图1-3 爆轰波产生的表面压力与反冲压力联合作用示意图。
综上所述,采用毫秒激光与纳秒激光联合打孔的方法,应当可以获得较高的质量迁移,进而可以提高打孔效率,更好的控制小孔轮廓及小孔质量。
双脉冲激光联合打孔研究现状(2):http://www.youerw.com/yanjiu/lunwen_75362.html