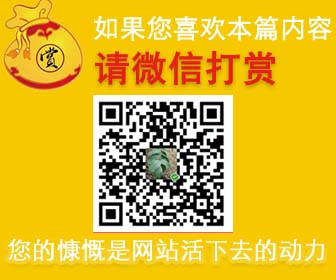
图 1.4 Gassman 设计的方形陶瓷预应力加载装置[18]
此实验装置的工作原理是,曲柄(1)在垂直权力线程(2)中旋转,这会带动滑动楔形块(3) 在其通道内上升或者下降。当滑动楔形块(3)在其通道内下降,一个横向的水平作用力将施 加于左副板(4)。厚钢性板的反向力通过嵌入式的负载单元和右副板传递给陶瓷,这样陶瓷 就完成了双轴压缩过程。此装置能对厚度为 5~9mm 的方形陶瓷块施加的预应力达到
500MPa。试验中对100100mm2 厚度 5、6、7mm AD98 方形陶瓷加压,陶瓷内部最大预应
力达到 400MPa。用此机械加压装置对方形 AD98 陶瓷施加不同预应力,并进行了初始速度 为 840m/s 的 7.62mm 穿甲弹弹道试验。不同预应力陶瓷 DOP 试验表明:随着预应力的增加, 剩余穿深线性减小。试验结果和 LS-DYNA 二维仿真结果对比结果表明,二者一致性较好。
马天宝[19]等(2015)开发了新的二维欧拉爆炸与冲击的仿真软件,并对长杆钨弹侵彻陶瓷 金属靶板进行数值仿真计算。在软件中嵌入了 JH-2 本构模型及高压本构方程,对不同厚度 陶瓷进行仿真,仿真结果与实验吻合度较好。Z.Fawaz[20]等,利用 LS-DYNA3D(非线性有 限元程序) 分别对穿甲弹垂直侵彻和倾斜侵彻陶瓷/金属复合装甲进行数值模拟和仿真分 析。研究结果表明:倾斜侵彻时,陶瓷金属层间应力和穿甲弹与陶瓷间应力值比垂直侵彻 时小,穿甲弹的侵彻更为严重。
热胀冷缩配合也被应用于预应力陶瓷的研究,其主要原理是利用金属和陶瓷的热膨胀系 数的差异实现对陶瓷预应力的施加。美国普渡大学航空航天学院 Sun 等[21]进行了大量多层 玻璃/铝复合板的实验研究。包义望(2000-2002)等[22]将熔化的铝合金浇在一个 600 摄氏度的 陶瓷块上(陶瓷块置于模具中间),铝合金在凝固的时候会对陶瓷块产生均匀的压应力。陶瓷 预应力大小由温度的差异和陶瓷与合金的弹性模量比值决定。最后,包义望等通过实验给 出了陶瓷及金属中应力的大小估算公式。
Kanel 设计的圆形陶瓷预应力加载装置[22]
俄罗斯科学院高能密度研究所,Kanel[23](2007)等设计了一套对脆性材料加载预应力的 装置,如图 1.5 所示,该加载装置能够对完成对陶瓷试样较大预应力的加载。
Meyer 等[24]用冷缩的办法来对陶瓷进行加压,用中子衍射(测量应变的一种方法)的方法 来测量陶瓷周向、径向的力。Anderson [25] 和 Orphal[26] 等先后都利用钛环冷缩的加载方式 对碳化硅陶瓷进行了相关的实验研究。实验中在陶瓷内部应力为 463MPa。并同时,根据实 验开展了相应的仿真分析,仿真计算出的碳化硅陶瓷产生的预应力和实验测得的应力是一 致的。Homquist[27] 等采用不同厚度预应力陶瓷和没有预应力装甲陶瓷进行侵彻实验,以研
本科毕业设计说明书 第 7 页 究预应力对弹道性能影响。一系列的仿真结果表明预应力陶瓷的弹道性能有所提高,预应 力陶瓷延迟后排陶瓷的破碎,提高陶瓷的弹道性能,但需要更多的工作来获得最佳的弹道
性能。
2未来的发展趋势
装甲陶瓷材料研究的重点是解决其韧性差的问题,其主要改善途径有:通过相变、过 颗粒弥散、纤维和晶须强韧化制造的陶瓷基复合材料[28]。目前研究方向为复相陶瓷、金属 陶瓷、玻璃陶瓷和塑料陶瓷几大类。对陶瓷材料进行表面处理可以降低其结构敏感性,通 常采用机械化学抛光、气相沉积法和激光表面处理、表面微氧化(对某些非氧化物的陶瓷如 SiC、Si3N4 等)的方法。现代技术中还有离子注入法,该方法可以提高氧化铝表面硬度 50%, 碳化硅和氮化硅弯曲强度 20%到 30% 。为进一步满足抗侵彻性能要求,在不增加密度和成 本的条件下提高装甲材料的弹道防护性能,主要技术途径包括开发梯度功能陶瓷装甲材料、 性能等于或优于 B4C 陶瓷的多相陶瓷、发展低成本 B4C 陶瓷、抗多发弹的树脂基复合装甲 材料、面密度小的轻质 SiC 复合材料和由陶瓷和聚合物复合材料组成的复合装甲等。论文网 装甲陶瓷材料国内外研究现状和发展趋势(2):http://www.youerw.com/yanjiu/lunwen_79294.html