2.7.5 腐蚀液一 32
2.7.6 腐蚀液二 33
2.7.7 腐蚀液三 34
2.8 硬度 34
2.8.1 设备 34
2.8.2 镶嵌 35
2.8.3 显微硬度 36
3 实验分析 38
4 结论 42
5 致谢 43
6 参考文献 44
1 绪论
1.1 引言
当今世界随着航空航天技术、军事装备和交通工具等领域的迅猛发展,对高性能金属材料特别是对高比强材料的需求日益增长。制备具有高比强度和良好塑性相匹配的材料,一直是各国材料科学和材料工程研究的热点,也是国际材料领域竞争最激烈的领域之一[1]。就目前各国的研究现状来看,合金化强化、形变强化、细晶强化和固溶—沉淀强化是常用的提升材料组织性能的主要途径。近年来,国际上本领域的大量研究成果证明,单纯依赖某一两种强化机制来提升材料的综合性能是十分有限的,将多种机制有机组合,不仅能充分挖掘材料的性能,也是材料科学发展的必然趋势[2-5]。大塑性变形(severe plastic deformation,SPD,以下简称“大变形”)就是在这样的背景下发展起来的一种用于提高材料性能的工艺技术。
大塑性变形工艺可以这样定义:在金属的成形过程中将超大塑性应变应用于一定体积的金属中以获得超细晶材料的过程。大塑性变形的本质是细晶强化——根据霍尔-佩奇关系(经验公式):σ=σ0+kd-1/2,在一定的晶粒大小范围内(即d在一定的范围内)晶粒越细材料强度越高[3]——与传统细晶强化的区别是把大塑性变形量施加于材料本身,根据具体实验的加工路径和加工条件,当材料晶粒小到一定程度之后(特别是晶粒达到亚微米及纳米尺度之后),起强化作用的往往并不单纯是细晶强化一种强化机制,而是多种强化机制共同参与作用,因此,大塑性变形有更高效的强化作用[6-8],由此引起了各国材料研究者的高度关注。
1.2 大塑性变形的基本原理
多晶体颗粒的屈服强度取决于颗粒的直径大小,可以用霍尔一佩奇公式表达:σ=σ0+kd-1/2,σ0表示摩擦应力,k为常数.
该式表明晶体的屈服强度的增加与晶粒的二次方根的减少成正比,与热处理等其他强化方式不同,由晶粒减小导致抗拉强度增加不会导致晶体的韧性下降。对此Azushima等学者引用了两个实例说明[9]:
弹性极限应力与纯铁中晶粒大小的关系在图1-3-1中给出,和霍尔-佩奇公式相类似,弹性极限应力和晶粒大小的二次方根成反比,从图上可以看出亚微米级的超细晶材料的弹性极限应力是商业纯铁的5倍,因此具有超细晶的传统结构金属由于它们具有较高的强度,在达到相同的使用强度条件下,使用的金属的量较少。
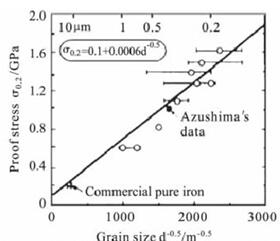
图1-2-1 纯铁晶粒大小与弹性极限之间的关系 图1-2-2 电线微元件样品的机械性能和材
料直径D/d的关系
从图1-3-2可以看出,用大塑性变形制造的电线样品的机械性能和电线的直径D与晶粒的直径d的比值成反比.当D/d小于100时,D/d越小,弹性极限应力越小.尤其,当D/d的比值小于5时,当D/d减小时,弹性极限应力下降的更快。从这些结果可以看出,D/d的比值只有大于100时,才能保证输电线材的安全性和可靠性。在多数情况下,电线(电缆)制品的直径D是确定的,故提高线材强度的最直接的方式即是细化晶粒(减小d);并且在这里还需要着重考虑线材的电导率因素,故诸如添加合金元素及弥散强化等会较大影响材料导电率的强化方式将受限使用,也使得细晶强化的作用体现得更明显。 2Al12铝合金轧后弯曲变形对其组织的影响(2):http://www.youerw.com/cailiao/lunwen_13308.html