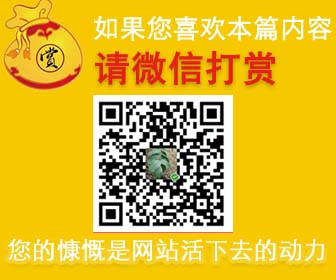
传统的筛板结构就是均匀在板面上钻孔,来自上层塔板的液体流过筛板,越过溢流堰进入下层板。筛孔塔板比泡罩塔的生产能力大10%~15%,板效率高15%左右,压降可降低30%左右,另外结构简单,造价低40%左右,便于清理检修。针对传统筛孔板入口鼓泡面积小、液面梯度大、气液有效接触区域有限等实际存在问题,各国逐渐改进都有如下进展与成果[1]。23982
(1) 国内塔板
由于国内板式塔的发展历史较工业发达的西方国家要短得多,因此国内以前使用的板式塔塔板,很多都是由西方引进并改造而成的。但是,随着国内化工设备研究水平的提升,国内的一些塔器生产商、研究院所及一些高校,已经研制出一批满足工业要求、高性能的新型塔板[2]。因其它类型筛板与本次毕业设计关系不大,故不再赘述。在此只介绍新型筛板塔板。新型塔板不仅能提高塔的生产能力、塔板效率,还能降低塔板压降和成本。因篇幅有限,在此只介绍DJ塔板以及95型大通量塔板。论文网
DJ塔板是由浙江工业大学在MD塔板的基础上开发的一种多降液管塔板,尤其适用于处理高液气比负荷操作和加压操作[3]。其中DJ-1型塔板的结构与MD塔板相似,改进点是突破了MD塔板降液管宽度小于200mm的限制,但是这种塔板的传质效率却比F1浮阀塔板和筛孔塔板都低,DJ-2型塔板在塔板上增设了导流装置,使进入塔板上的液体分布均匀,减小了滞留区面积,塔板效率与筛孔塔板相当,DJ-3型塔板在降液管两侧增加了薄层规整填料,当气液负荷高时可以减少雾沫夹带,而当气液负荷低时填料层可起强化传质作用,塔板效率比筛孔塔板高10%~15%。
南京大学开发的95型大通量塔板,因该板的有效传质区面积约占全部塔板面积的95%而得名,其采用月牙型、流线型溢流堰或三角型纵剖面的拖尾式设计,在加入导流板后可基本消除涡流区,使流形趋于合理[4~5]。
(2) 国外塔板
国外使用板式塔的历史已经超过百年,因此,在板式塔的设计及塔板的研究上比国内要先进。随着工业生产节能、高效、环保的需要,国外也研制出一批新型的塔板。
MD塔板,多降液管筛板(Multiple Downcomers Sieve Tray),最早是美国联合碳化物公司在20世纪60年代开发而成。塔板上设有多根矩形降液管,且降液管挂在气相空间,出口堰的总长远远大于一般塔板,每相邻两板的降液管互成90°排列,液流流程短。此后又出现了结构优化的多降液管精馏塔板,克服了气液接触时间的不一致性[6~7]。
NYE塔板是格单奇公司开发的高通量塔板,1991年获得专利。塔板上没有受液盘,降液管悬挂设置,整个板面都为开孔区域[8]。VORTEX塔板是SULZER CHEMTECH公司开发与生产的专利产品,结构上设计了一种独特的悬挂式防旋涡降液管,增大了有效鼓泡区面积,但塔盘结构比较复杂。
SLIT塔板[9]由瑞士KUHNI公司在筛孔塔板的基础上开发成功,这种塔板在结构上以一对细缝代替筛孔,同时穿过细缝的气体沿水平方向与液体接触,雾沫夹带明显减少。目前一共有A、B两种类型,虽然降液管的设置不同,但操作弹性相当,B型较A型液体负荷大得多。此类塔板尤其适用容易起泡的体系或带有固体颗粒的物料。
新型垂直筛板(NVST)是由日本三井造船株式会社于1968年前后开发成功的,其接触单元罩筒结构如图1.2所示。罩筒上有盖板,有效抑制雾沫夹带,罩筒底部与塔板留有缝隙,四周开有筛孔,中间有一隔板把罩筒一分为二,以防止进入罩筒内的液体发生撞击。从下一块塔板上升的气体流经罩筒,把罩筒底部的液体拉成液膜,气液同时在罩筒内上升,然后从筛孔水平喷出。该塔板不仅处理能力大,而且气体在整个过程要经过拉膜、提升、破膜、混合、喷射分离等过程,在罩筒内外经过2次传质,传质效率高 塔板国内外研究现状:http://www.youerw.com/yanjiu/lunwen_17278.html