4.2.1.2无线传感器发展现状20
4.2.2无线传感器监测技术 23
4.2.2.1无线传感器监测技术简介24
4.2.2.2数控机床无线监测技术的发展现状24
4.3 设计内容 25
4.3.1 系统方案分析与选择论证 26
4.3.2 主要芯片介绍和系统模块硬件设计 29
5设计小结36
6致谢37
7参考文献38
1 绪论
1.1. 课题的研究背景
近几年来,随着数控技术的不断发展,机械零件的加工精度也得到了飞速的提高,但是在工业技术的不断发展的推动下,人们对机械产品的质量也有了越来越高要求,因此对数控机床的加工精度提出了巨大的挑战。一般来讲,影响数控机床加工精度的误差来源主要分为以下几种:机床热变形误差、机床零部件和结构的几何误差、机床伺服误差和切削力等引起的振动误差等等。
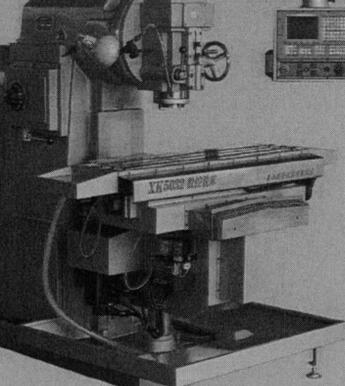
图1.1 数控铣床
经过大量的研究发现, 40%~70%的加工制造误差是由机床热变形引起的。另一方面,机床制造技术的飞速发展,使机床的制造精度有所提高,结构的几何误差等也因此得到了较好的解决,这就使得热误差成为影响机床加工精度的最重要因素,也是最令人困扰的问题之一。采取怎样的措施能够有效减小机床热误差这个问题深深困扰着人们,也是很多学者一直以来广泛研究讨论的课题。目前最常用的是误差补偿法,即设计一种新的误差来抵消原始误差。这种方法投入的费用比提高机床本身精度或者购买高精度机床的费用要低得多。基于误差补偿软件的补偿方法是减小机床误差,达到高精度加工这个方法已经被研究者们证实是潜在的重要途径。尽管学者们在这方面进行了广泛的研究和探讨,但热误差补偿模型是基于对数控机床温度场有效检测的前提下来建立的,且影响机床热变形的原因多种多样,因此全面掌控机床整体温度状态是一件极端困难的事。要做到对机床温度的有效测量,必需在对机床的热行为有明确的认识前提下,构建一个合理的温度测量系统。
1.2课题的研究意义
铣削温度是铣削过程中一个重要的理论参数。在铣削过程中,热效应影响具有十分明显的优势。铣削面可等效为热源,对即将进入铣削面的金属进行持续的加热。使得金属的温度升高,抗剪强度降低,因此降低了剪切力,减少或避免了金属材料的加工硬化。另一方面,金属表面薄层的温度较高使得材料屈服应力较小,因而进一步使刀工摩擦力减小。切削温度使切削力降低,切削过程也因此变得更加容易。根据萨洛蒙博士的切削温度理论,刀具寿命存在一个“死谷”,当切削速度超过“死谷”,刀具寿命明显增加。切削速度的提高使传入工件的热量明显减少,工件容热也因此减少,因此温度下降较快,加工表面的温度很快变得稳定。工件温升较小有利于得到较为完整的加工表面和有效抑制因工件热变形而导致的加工精度的降低。切削温度的测量有两种,接触式测量和非接触式测量。接触式测量方法主要分为自然热电偶法和人工热电偶法为。自然热电偶法通过测量刀具和工件在切削过程中产生的热电动势,从而获取温度。但是测定的是切削区域的平均温度,而不是切削区指定点的温度。而且切削温度—自然热电偶得到的温度—电压值曲线对于刀具与材料的唯一性,增加了测温过程中的困难。
人工热电偶法可测量刀具、切削和工件上的指定点温度。而且对于标准的人工热电偶不需要对其温度值进行标定。但是人工热点偶存在一个缺点,在测量过程中需要将其埋放在被测物体内,这破坏了物体本身热量的分布,测量过程中产生的误差也因此而增大了。因为传统的人工热电偶测温方式对热电偶布置、安装有严格要求,并且须要预先在工件上加工出符合要求具有一定的形状和尺寸精度的小孔,这种测试方法不适合于切削温度监测走向工程实践,只适合于金属切削理论的研究。接触式测量方法虽然可以准确的得到所要测量位置的温度,但其本身装置安放的困难和其测温信号的延迟性限制了它在一些场合的应用。 zigbee铣削红外成像无线测温系统设计(2):http://www.youerw.com/zidonghua/lunwen_22443.html