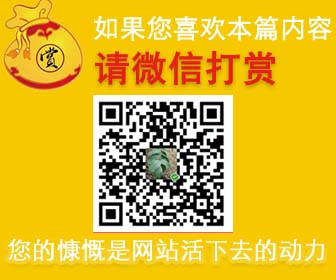
5.2.1 加工过程的监测 30
5.2.2 加工时出现的问题及解决 31
5.3 后处理流程 32
5.3.1 查看钻削的变形过程 32
5.3.2 温度的变化 32
5.3.3 最大应力的分部 33
5.3.4 最大应变的分部 34
5.3.5 刀具磨损分部 34
5.3.6 钻头的扭矩变化 35
5.4 本章小结 36
结论与展望 37
致谢 38
参考文献 39
第一章 绪论
1.1 选题背景及意义
1.1.1 选题的背景
随着科技的发展和制造水平的不断提高,制造对象复杂程度越来越高,深孔加工在机械加工中占有的地位越来越重要。由于一些关键的技术问题还没有很好的解决,深孔加工仍然是机加工中的瓶颈工序。因为深孔加工和普通孔加工的方式不同,深孔加工时环境更为复杂、限制因素更多,所以需要加工前的试验得到相对较好的参数。从行业普遍认为的来看,深孔即为孔的长径比大于10的孔,而一般加工中深孔的长径比可能超过100。例如油缸孔、轴的轴向油孔等。
深孔加工起源于军工生产领域,主要用来生产枪管和炮管的内膛。随着我国经济技术的发展和科技的进步,深孔加工应用范围越来越广,涵盖了整个制造业,尤其应用在高新技术产业领域,以航空航天制造业为最。该领域的深孔加工的范围越来越广,技术难度越来越高,反过来推动深孔技术的创新和发展。
1.1.2 选题的意义
深孔加工过程中的切削参数改变引起的钻削力的变化是影响加工效率、加工表面质量和加工成本的重要因素。如何能够在实际加工前对加工做出适当的模拟和仿真将关系到加工时的效率和质量。这就使得多个行业对深孔加工技术创新的需求,这种需求将导致更多的研究机构来研究深孔加工的仿真和创新,同时是对我国落后的工艺设备、技术人员的一个重大挑战。所以,深入开展深孔加工技术的研究与创新,将对我国制造业产生重大影响。
因此,本文针对机身零件的关键部分进行了孔加工的模拟与仿真,选取了典型的深孔利用三维有限元仿真软件DEFORM-3D进行了加工仿真模拟,得到加工以后产生应力、应变和温度场的分部情况,为实际加工提供了依据。
1.2 深孔加工仿真技术的现状和存在的问题
对于深孔加工的工艺研究由来已久,从美国人在18世纪发明扁钻以来,对于深孔加工的研究从来没有停止过。在20世纪初,深孔加工技术因为战争对枪炮的需求而快速发展。而深孔加工中由于巨大的工作量以及高昂的成本(约占整个加工过程的成本的四成以上),使它成为金属切削加工中投入产出比最大,难度最高的领域。
1.2.1 国内现状
1.2.2 国外现状
1.2.3 存在的问题
深孔加工工艺特点主要有如下三点:
(1)钻头容易引偏:钻头的刚性很差,且定心作用也很差,因而导致钻孔时的空轴线歪斜。
(2)排屑困难:钻孔时由于切屑较宽,宽屑槽尺寸又受到限制,所以排屑困难。切屑与孔壁发生较大的摩擦、挤压,会拉毛和刮伤已加工表面,降低表面质量。特别是当切屑阻塞在钻头的容屑槽里并卡死钻头时,易将钻头扭断。 DEFORM-3D软件仿真深孔加工过程(3):http://www.youerw.com/jixie/lunwen_54857.html