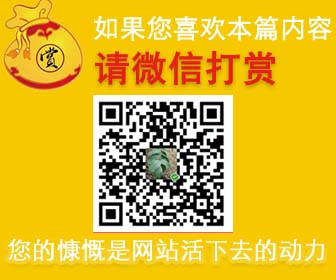
参考文献 30
第一章 绪论
1.1 研究背景
在切削工件时,刀具切下切屑,自身也会发生损坏。切削刃由于自身所处的位置的特殊性,往往会成为刀具上最容易损坏的部位。刀刃发生磨损或者破损,不仅仅会严重的影响到零件的尺寸加工精度,也会影响已零件表面的加工质量, 还会对车床造成一定程度的损坏。切削加工的生产率的阻碍主要是刀具寿命,为了提高刀具寿命,很多人对此进行了实验研究,在史蒂文森和史蒂芬森的切削试验中,研究了不同进给率下的刀具温度以及应变率,蒙哥马利和阿尔滕塔什研究了动态铣削力,目前,国内外相对较少的研究已经完成,使我们对这些刀具的切屑形成机理,刀刃的几何形状对切削参数的影响得到更好的理解。但在以前的研究中, 研究人员们为了研究方便,常常将刀尖的形状抽象成理想锋利的。可是在实际切削过程中,刀刃在切削力、切削温度和各种化学作用下很快就会发生磨损,所以理想锋利的刀尖是并不存在的。
本论文,选取了“基于有限元分析的刀具刃形优化”这个课题进行研究,这对于我们改进优化刀具刃形,提高工具寿命,提高零件表面加工质量,提高生产率具有很重要的意义。
1.2 刀具磨损形式
刀具磨损在切削加工过程中是不可避免的现象,刀具磨损过快或发生非正常磨损(即破损),必然会影响零件表面的加工质量,使刀具消耗加快,使生产效率降低,带来了很多不必要的加工花费。
理论上,影响刀具切削性能的主要因素有:刀具几何参数(前角,后角,主副偏角,刃口圆弧半径等等)、刀具材质、切削用量、工件材质及其机械性能等等。这些因素中工件材质属于不能控制的因素,改变其它因素的属性可控制刀具的磨损形式及磨损率,例如可通过改变工件材料的热处理状态来改变工件材料的机械性能,从而对刀具的磨损进行影响;另一方面,合理的刀具材料的选择和刀具几何参数变更也可改善刀具磨损效率;生产上面一般还可以通过切削用量的合理选择来减少刀具磨损率,从而提高刀具的使用寿命。
刀具的失效形式可分为正常磨损和非正常磨损两大类:正常磨损是在切削过程中,刀具切削刃、前刀面、后刀面分别与加工表面、切屑和已加工表面接触,在接触区里受切削力和切削热的耦合作用,并发生强烈的摩擦产生的,切削刃、前刀面和后刀面都会发生磨损。正常磨损时,刀具的磨损量随切削时间增长而均匀地增加。刀具的前期破坏或使用过程中的剥落、卷刃、突然崩刃或刀片的整个破裂都称之为不正常磨损。
正常磨损主要是由以下原因造成的:①磨料磨损,切表面的灰尘或工件存在硬点(如碳化物颗粒和建立起来的边缘片段)在工具表面(前刀面和后刀面)上造成磨损。低速切削,磨损原因不明显,高速切削,磨料磨损是刀具磨损的主要原因;②粘着磨损,切削工件材料沿刀具前刀面运动,切削工具上的氧化层和其他吸附膜表面的破坏,特别是由工件材料内部所造成的磨损。切削速度和粘着磨损之间也存在着复杂的关系,粘着磨损主要发生在一般中等切削速度范围内,刀具材料和工件之间的作用力,刀具材料和工件材料以及刀具材料的硬度比都对黏着磨损率有影响;③扩散磨损,因为工件和刀具前刀面,在高温度,高压力较大的接触和化学活性,化学元素扩散到接触表面使他们相互改变对方,对材料的化学成分和结构造成影响,造成磨损的形成,扩散磨损和粘着磨损同时发生。由于每个元素的扩散速度是不同的,所以扩散磨损和刀具材料的成分有很大的关系的程度,除了这个,速度和温度的扩散磨损也有很大的关系,温度越高,扩散速度快,所以扩散磨损主要发生在高速切削速度范围。这就是为什么刀具的磨损是非常复杂的,涉及机械,热,化学,物理和其他因素的影响,在不同的工件材料,刀具材料和切削条件下,磨损和磨损程度的原因是不同的,对于一个给定的工件材料、刀具材料,切削温度对刀具磨损的决定性影响。 Deform基于有限元分析的刀具刃形优化(2):http://www.youerw.com/jixie/lunwen_56183.html