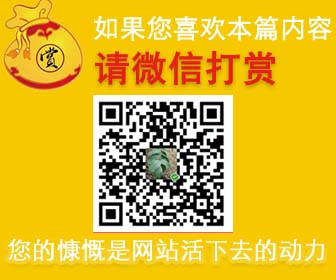
陶瓷材料微波烧结的研究现状微波烧结技术的第一次提出可以追溯到上个世纪50年代,由Tinga WR等人发起这个概念[7]。大多数学者认为,此后,这种烧结技术经历了三个发展阶段。上世纪70年代中旬到80年代初,为实验初步研究阶段,其研究目标大多集中在材料的对微波的吸收能力以及低温性;第二阶段,80年代中期到90年代中期,为研究发展阶段,深入研究集中表现微波理论运用于不同材料,系统结构优化设计,介电参数,数值模拟,烧结工艺等方面。第三阶段,90年代后期到现在,称为产业化发展阶段[4]。采用微波烧结技术制备的陶瓷材料具有较高的相对密度、硬度和强韧性,特别是烧结纳米陶瓷材料的有效方法[8, 9]。49812
目前为止,差不多全部的陶瓷材料已经使用微波工艺,然而产业化发展远不如研究领域如此生机勃勃[10]。官方公示,也只有Al2O3,ZnO,WC/Co,V2O5等陶瓷材料实现了小规模工业化生产。
具体陶瓷材料的微波烧结工艺和力学性能具有相当不同凡响的表现。通过对微波烧结Al2O3/SiC纳米复合陶瓷[11]实验的一系列比较,可以得出:加热方式对Al2O3/SiC纳米复合陶瓷的力学性能有显著的影响,但在1600℃时Al2O3和SiC的介电损耗系数增大,使得材料力学性能有所下降。采用微波加热对Al2O3/SiC纳米复合陶瓷的强度和韧性显著改善,是因为微波能使得被烧结样品的活化能下降,促进固相烧结过程中原子扩散,从而提高了Al2O3和SiC 的固相溶度,导致提高纳米SiC对Al2O3的增韧补强效果。此外,这种烧结方式是整体均匀加热,得以实现材料中大区域的零梯度均匀加热,降低物料热应力,适当减少Al2O3/SiC纳米复合陶瓷的内缺陷,使物料内部更致密,晶粒更细化和分布均匀,因此微波烧结可得到高致密性、高强度和高韧性的Al2O3/SiC纳米复合陶瓷。
微波烧结的发展趋势
陶瓷刀具的微波烧结技术正逐渐从研究所里走向工厂,为此,这也注定了陶瓷刀具的微波烧结的发展趋势必然要符合产业化生产趋势论文网。小批量生产甚至是单件生产的科研生产模式绝对不能运用于工厂化批量生产模式。这就要求科研人员要从生产者的角度考虑生产模式,推广技术以及管理的革新,以求做到尽可能的大批量生产陶瓷刀具,使得对于陶瓷刀具的微波烧结研究更具有科研意义。
因此未来的发展趋势主要有以下几个方向。首先可以考虑对原材料采取预处理、能量调配、高效介质材料的开发来解决材料自身的问题,如热膨胀系数大、导热效率低、尺寸过大,微波吸收吸收低等[12]。其次,通过对微波场的设计来提高场区域的均匀性,主要有混合场、多模腔场方案[13]。接下来,陶瓷材料介电性能的数据库建设及理论发展。温度测量与控制,提高温度测量与操作的自动化、智能化程度也是大有潜力的[14,15]。最后,对设备的联合开发,制造出大面积的均匀微波场,降低设备价格与维护费用。
陶瓷材料微波烧结的研究现状和发展趋势:http://www.youerw.com/yanjiu/lunwen_52930.html